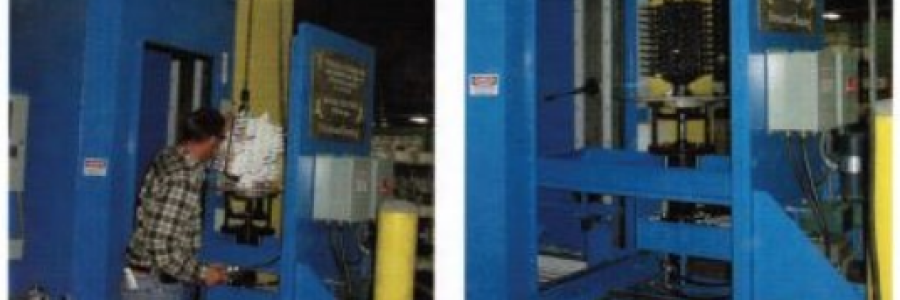
Wisconsin Precision Casting, Inc. Chooses Waterblast Casting Cleaning Method
Automation Solidifies Waterblast as a Competitive Investment Casting Cleaning Method
Some companies choose mechanical knockout, caustic cleaning, sand blast, or shot blast methods for cleaning investment casting. While the use of caustic chemicals or brute force to clean and remove investment immediately prompts concerns about safety and waste, the use of waterblast technology instantly makes sense. According to INCAST magazine, Wisconsin Precision Casting, Inc. Vice President-Manufacturing Cliff Fischer said former experience, new technology, and automation were among the factors influencing the company’s decision to invest in the waterblast casting cleaning method for its manufacturing operations.
“I had prior experience with waterblast cleaning of investment castings and knew the potential cleaning capabilities of using the technology,” he said. “However, Wisconsin Precision could never truly investigate waterblast cleaning, mostly because our plant is situated in an area that requires all of our process waste-water to be hauled off site due to the fact that there are no city sewers in the vicinity. While at a trade show in Chicago, we saw a filtration unit that utilized 100% recycled the water for a water-jet cutting table. This would give us the opportunity to customize the filtration for a waterblast unit. thus having no process waste-water to dispose of, Another reason for deciding to purchase a waterblast unit was to help in the safety and productivity of our rough-clean process.” he added. Fischer noted the automated equipment he is using (Triplex TRX-1250) features random automatic nozzle movement and frees operators for other tasks. “We waterblast 98% of the trees using the automatic waterblast unit,” he said. The only molds that we do are the extremely fragile, thin-walled aluminum castings that will still deform even using a lower pressure nozzle.”
“We still do some secondary cleaning but this automated system has greatly reduced the need for secondary operations,” he commented. “We have ‘stepped down a notch’ with our secondary cleaning operations. For example, we do have an in-house molten salt bath for removing shell because it is expensive and takes a lot of time. We use a contract house to clean those difficult-to-clean castings.” Aside from waterblast, Wisconsin Precision uses several secondary cleaning options. The company has an in-house aqueous cleaning process. which is not nearly as aggressive as the molten baths. but used for small amounts Of shell removal. Also included are in-house shot-blasting. hand sand-blasting and tumble blasting. “Since we have really dialed in our waterblast cleaning process, most castings have stepped down a level of post waterblast cleaning,” he said.
Fischer indicated Wisconsin Precision is able to go directly from waterblast to cut-off. “Typically, we have one person working the waterblast/cut-off cell. While a mold is cleaning in waterblast, the operator will cut another mold. “On the majority of our castings. the waterblast unit will remove 90-95% of the shell, unless there is a deep core, holes, or pockets that are not exposed to the nozzle,” he said. “It the water can see it, it will come off! We have even designed secondary fixtures to re-orient casting after cut-off so that the water can get to features that it could not see while on the mold. And once the system is programmed, molds come out the same way every time. We can remove the shell from crack-prone alloys now where we could not mechanically knock them out before.” A welcome by-product of waterblast is a drastic reduction of dust and noise in the rough-clean area. “We are very focused on safety, and the waterblast unit has greatly reduced body fatigue on our employees versus our old mechanical knock-out system,” Fischer said. “I believe waterblast is a viable cleaning process for castings, although a bit more development on water recycling and programmable nozzles would finish the development off completely,” he concluded.
Triplex Systems’ continuous pursuit of perfection has driven the waterblast casting cleaning method to the forefront, increasing safety, improving efficiency, and automating processes.