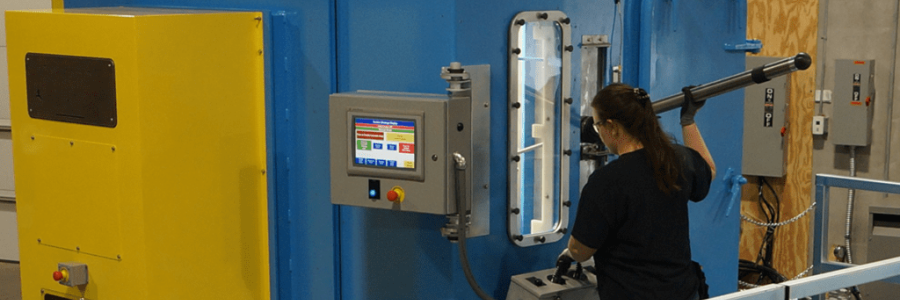
Benefits of Triplex Systems Waterjet Cleaning Equipment
Foundries Benefit from Triplex Systems Waterjet Technology
There are many benefits associated with using our equipment for your casting cleaning needs.
-
A big pay back would be in hazardous waste reduction, by greatly reducing the use of hot caustic for removal ofshell material. With the TRX-1250CAM the automatic waterjet process alone will easily remove 85% to 90% of ceramic from the castings. This first cleaning cycle we refer to as the primary waterjet cleaning cycle, which includes waterjet knock-out and gross overall removal of shell material. With the TRX-1250CAM you can then select the Manual cleaning cycle and remove the remaining shell material from 90% to 100% cleaning. This we refer to as the secondary cleaning cycle. If there is a small amount of ceramic left it would reside in pockets or passages that the waterjet cannot hit directly. Ceramic remaining in pockets will usually come off downstream during casting finishing operations. The only primary requirement for hot caustic would be ceramic in deep passage or preformed internal ceramic cores. I have many customers that have eliminated or significantly reduced the use of hot caustic and the hazardous waste associated with this chemical process.
-
Another good benefit of using waterjet casting cleaning is eliminating silica dust by virtue of the wet process. We have been promoting silica dust reduction with our process for 25 years.
-
Our waterjet process eliminates the need for mechanical knock-out, and the potential for stress cracking castings, noise and severe dust associated with this mechanical process. The waterjet process also eliminates or significantly reduces the need for shotblast for ceramic removal This will also reduce maintenance downstream at your baghouse.
-
The waterjet process not only cleans the castings it also cleans the runners so they are free of ceramic. This has a positive effect downstream by having clean sprues and runners extends the life of abrasive cut-off wheels during cut-off and after cut-off eliminates secondary cleaning of the re-melt.
-
The TRX-1250CAM is a complete wet process finishing department, that can be operated by one person. If you arrange the TRX-1250CAM with a Gator Cut-Off Saw in a workcell, one operator can run both machines. Example: While tree is in automatic cleaning cycle the operator can be cutting off with the Gator Cut-Off Machine. Reference Wisconsin Precisions Waterjet Cleaning and Cut-Off workcell. This would be a potential major labor savings.
-
Safety and Ergonomics, is an important consideration. When using a lifting device for loading trees the operatorhas no body stress. When operating the manual mode the lance moves freely with no loads to the operator and easy electronic joystick controls. The operator simply looks, points and uses fingertip joystick controls. The machine is electronically integrated with safety controls that protect and prevent the operator from making operational mistakes.The equipment including the automatic mode can be run and programmed by any operator. The only information required to input is the height of the tree and the cycle time. The patented automatic nozzlemovement program does the rest. So in short you do not require a programming engineer to operate the TRX1250CAM.